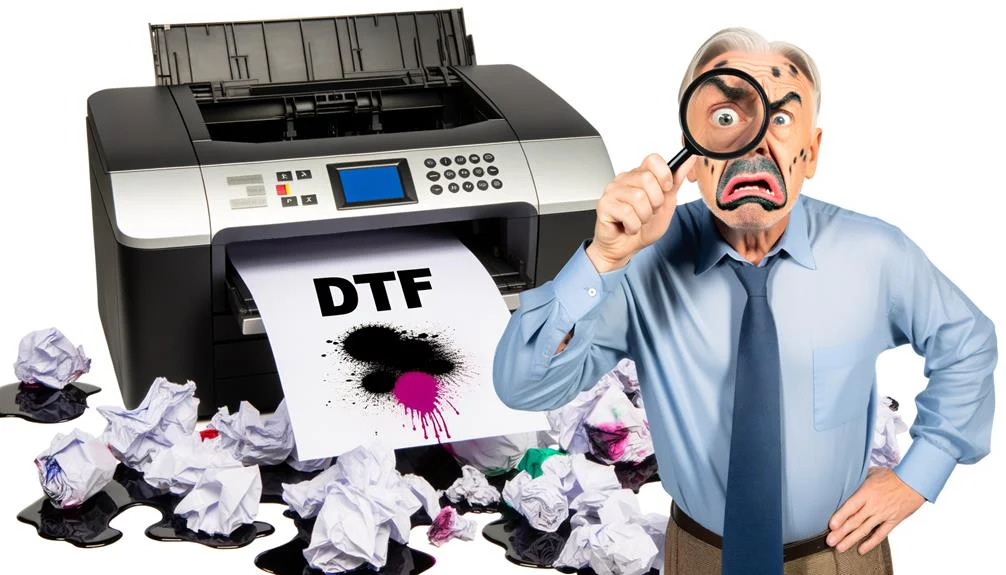
Introduction
Direct-to-film (DTF) printing has become a top choice for high-quality prints on various materials. Whether you’re in custom apparel or personalizing products, DTF offers vibrant colors and fine details. But, some DTF printing mistakes can ruin the print.
DTF printing mistakes are common, and we shall give you insight into how to avoid them. Understanding and fixing these DTF printing mistakes will help you improve your prints, reduce waste, and deliver better results.
Whether new to DTF or experienced, these tips will help streamline your work and boost your printing business.
1. Choosing the Wrong Transfer Paper
Choosing the wrong transfer paper is one of the prevalent DTF printing mistakes. Low-quality or incompatible paper can lead to faded, blurry prints or trouble transferring ink to fabric.
How to Avoid This Mistake:
Use high-quality transfer paper designed for DTF printing. Ensure it’s compatible with your ink and fabric. Different papers are better for light or dark materials, so select the right one for your project.
Store your paper in a cool, dry place. Temperature and humidity can affect the quality. Using the right paper will give you more precise, more durable prints.
2. Incorrect Printer Settings
Printer settings are crucial for high-quality DTF prints. Incorrect settings can cause misalignment, poor color, or excessive ink. These issues lead to blurry images, uneven ink distribution, or designs that don’t stick well to the fabric. This is also one of the most common dtf printing mistakes people make.
The settings control how the ink is applied to the transfer film and the final print on the fabric. Getting the settings right helps produce sharp, vibrant, and consistent prints.
Avoid This Mistake:
- Calibrate Your Printer Regularly: Calibration ensures that your printer settings align with the materials you’re using. This prevents misalignment and ensures accurate prints. Regular calibration keeps your prints sharp and precise.
- Follow Manufacturer Guidelines: Always follow the printer’s recommended print speed, temperature, and ink type settings. These settings are optimized for your printer and ink, ensuring the best results. For example, printers often need specific temperature settings to prevent ink clogging and uneven application.
- Adjust Settings for Different Materials: Different fabrics and transfer papers need different settings. Polyester handles higher temperatures better than cotton, so adjust the heat accordingly. Fabric texture also affects how ink is absorbed, so tweak the print speed or ink levels to suit the material.
- Test Prints: Test prints help you check color accuracy, resolution, and print quality before doing an entire run. This lets you catch any issues like color mismatches or ink bleed early. After testing, adjust the settings to improve the results.
- Control Ink Saturation: Too much ink causes muddy prints and bleeding, while too little results in faint designs. Adjust ink saturation to find the right balance for vibrant, sharp prints. Most printers let you fine-tune ink density for better control.
- Check Print Head Alignment: Misaligned print heads cause blurry prints or uneven designs. Regularly check and adjust the alignment to avoid these issues.
You prevent errors like ink overflow and misalignment by managing your printer settings. With some testing, you’ll find the best settings for each material and design. Correct settings lead to better prints, less waste, and a smoother printing process.
3. Inadequate Pre-Treatment of Fabrics
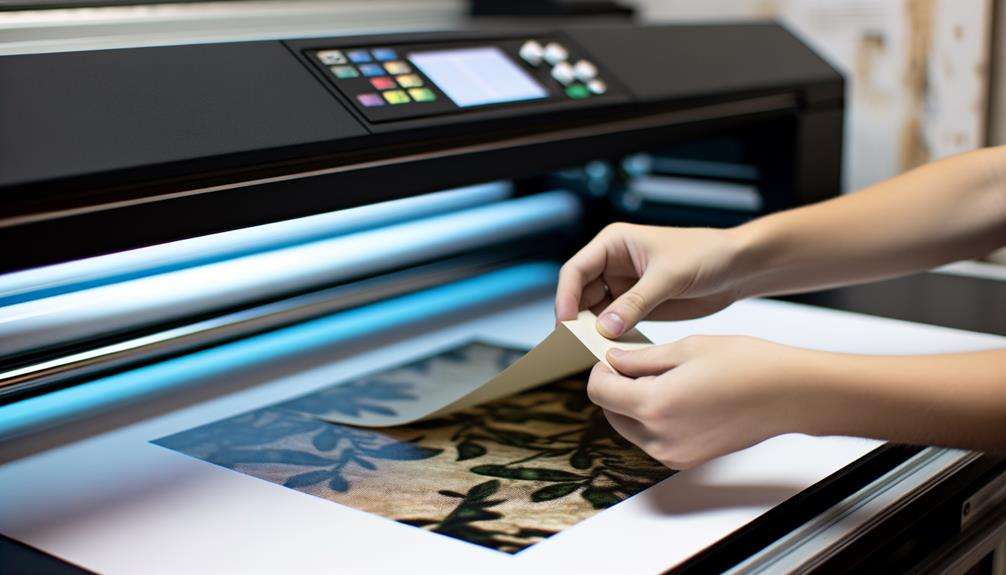
Not pre-treating fabric properly is another mistake. The ink won’t bond well without it, causing prints to fade or peel.
How to Avoid This Mistake:
Pre-treat fabric with the right solution before printing. Each fabric needs a different treatment, so follow the guidelines carefully. Cotton, polyester, and blends may all need other products.
Allow the fabric to dry completely before printing. Proper pre-treatment ensures better ink adhesion and more vibrant prints.
4. Failing to Cure the Ink Properly
If the ink isn’t fully cured, it may smudge, fade, or peel off after transfer.
How to Avoid This Mistake:
Ensure proper curing of your prints. Use a heat press at the recommended temperature, typically 160-180°C (320-356°F), for 15-20 seconds.
Adjust the temperature and speed of a conveyor dryer to match your needs. Always test the curing process with sample prints to avoid issues later.
5. Poor Color Management
Color mismatches are common if you don’t manage your colors correctly. Your final print may look different from what you see on screen.
How to Avoid This Mistake:
Calibrate your printer regularly. Use color profiles and make sure your monitor is calibrated, too. Work with design files in the correct color mode, such as RGB or CMYK.
Invest in color management tools for more consistent prints. This ensures the colors you see on the screen match your final prints.
6. Using Low-Quality Inks
Low-quality links can lead to faded prints and may clog your printer’s head.
How to Avoid This Mistake:
Use high-quality DTF inks. They are formulated for better adhesion and vibrant results. Choose inks from reliable suppliers.
Store ink in a cool, dry place to preserve its quality. Don’t use expired or poorly stored ink.
7. Not Preparing the Film Properly
Failing to clean the transfer film can result in prints with dust or debris, causing imperfections.
How to Avoid This Mistake:
Wipe down your film before printing. Use a lint-free cloth to ensure it’s clean and free from dust. This helps avoid marks on the final print.
Keep film stored in clean, dry conditions to prevent contamination.
8. Underestimating Print Resolution
Low-resolution designs can result in blurry or pixelated prints.
How to Avoid This Mistake:
Ensure your designs are at a resolution of at least 300 DPI. If you use vector graphics, ensure they’re scaled correctly to avoid pixelation.
High-resolution designs will give you sharper, more detailed prints.
9. Ignoring Print Time and Temperature Control
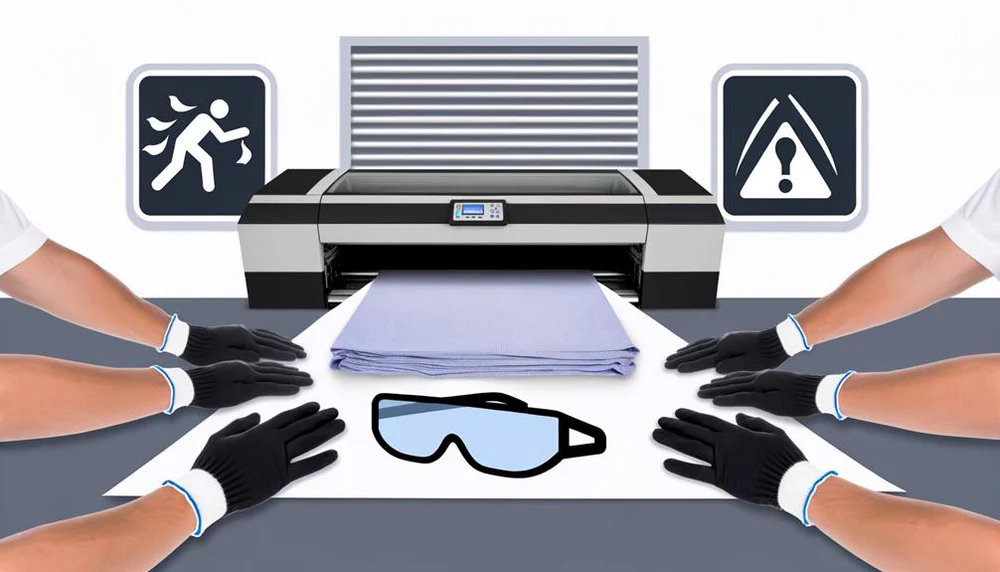
Incorrect print time and temperature can cause incomplete transfers or poor adhesion.
How to Avoid This Mistake:
Follow the recommended print times and temperatures for each material. Typically, a heat press should be set between 160-180°C, and the time should be 15-30 seconds.
Check the pressure and heat distribution. Inconsistent pressure can cause parts of the design to peel off.
10. Overloading the Film with Ink
Too much ink on the film can lead to smudging, ink bleeding, or uneven prints.
How to Avoid This Mistake:
Adjust your printer settings to apply the right amount of ink. Monitor ink output closely to avoid excess. If you notice pooling, remove the extra ink.
Excessive ink can also affect curing, so always aim for a balanced application.
11. Skipping Regular Printer Maintenance
Neglecting printer maintenance can lead to clogged heads, poor print quality, and breakdowns.
How to Avoid This Mistake:
Clean your printer regularly, especially the print heads. Use the cleaning program if your printer has one. For stubborn clogs, use appropriate cleaning solutions.
Check for worn parts like ink cartridges and replace them before they fail.
12. Ignoring the Importance of a Clean Environment
Dust and debris in your printing area can contaminate your prints, leading to marks or color inconsistencies.
How to Avoid This Mistake:
Keep your workspace clean and dust-free. Consider using air filters if necessary. Always handle materials like transfer papers and films with clean gloves.
A tidy workspace will improve print consistency and reduce defects.
13. Not Testing Designs
Jumping into large print runs without testing can lead to wasted materials and missed expectations.
How to Avoid This Mistake:
Always test your designs on sample fabrics before committing to a print run. Check for color accuracy, print quality, and design clarity.
This step helps you identify any issues and adjust early, saving time and materials.
14. Not Considering Fabric Type and Compatibility
Different fabrics require different settings and materials. Using the wrong fabric can cause poor ink adhesion.
How to Avoid This Mistake:
Know your fabric. Cotton, polyester, and blends each need specific settings. Test small prints to find each fabric’s correct ink, paper, and treatment combinations.
Pay attention to the fabric’s texture and weight. This ensures better results and fewer mistakes.
15. Failing to Track Production and Inventory
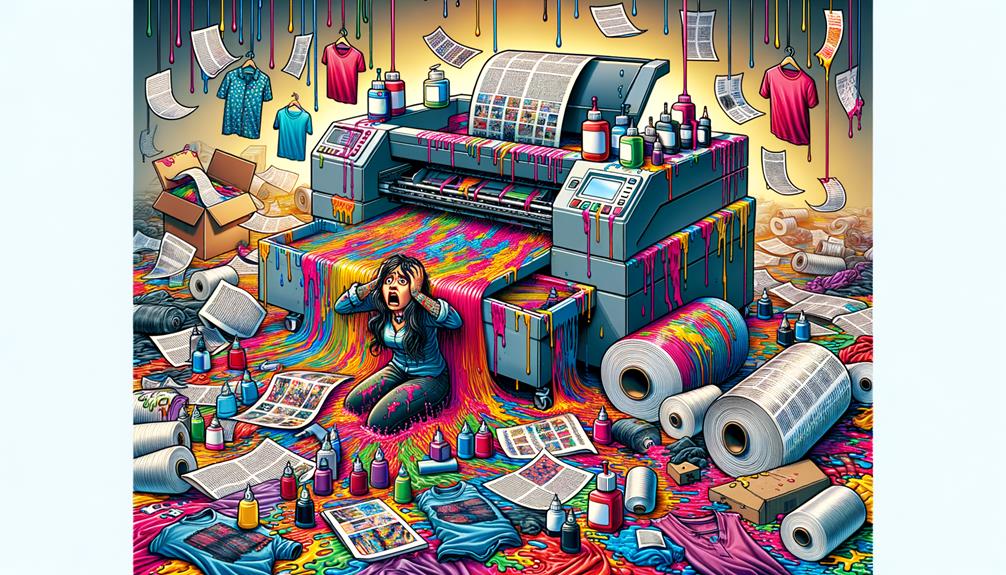
Not tracking your inventory or production process can lead to shortages, missed deadlines, or wasted materials.
How to Avoid This Mistake:
Use an inventory management system to keep track of your materials. Check ink levels and transfer paper stock and other supplies to avoid running out at crucial moments.
Track production details like settings and materials used. This makes future projects smoother and ensures consistency.
Conclusion
DTF printing offers excellent potential for producing vibrant, durable designs. However, avoid common mistakes as they are vital to ensuring quality. You can improve your results by using suitable materials, calibrating your printer, pre-treating fabrics, and curing ink properly.
Regular maintenance, testing designs, and keeping a clean workspace are also crucial. You can consistently create top-quality prints by staying vigilant and mindful of these tips. This proactive approach will save time, reduce waste, and help you grow your printing business.