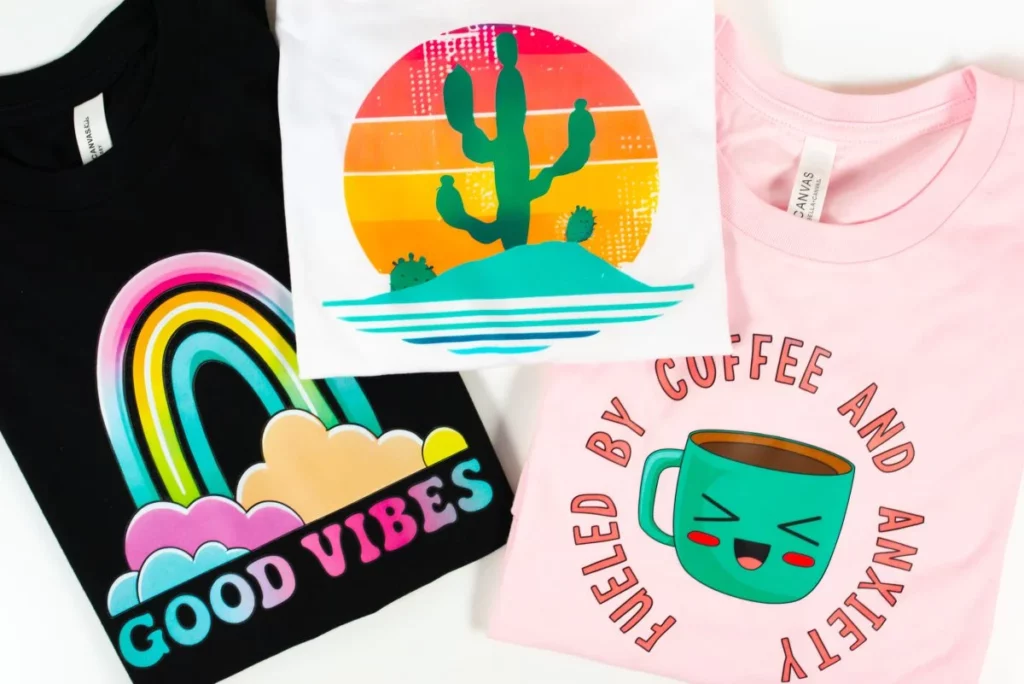
Introduction
Enter the vibrant world of DTF (direct-to-film) printing! Where imagination is limitless, and colors come to life! Get ready for an exciting voyage if this is your first time dabbling in printing.
DTF is at the front lines of this breakthrough in printing technology. Today, it’s more than just putting ink on paper. it’s about using your imagination to create vivid, real images on a variety of surfaces.
Read on as we solve the puzzles surrounding DTF printing in this beginner’s guide!
What is DTF Printing?
What’s the deal with DTF printing, then? Imagine a method that achieves unparalleled color accuracy while also capturing your design. DTF’s brilliance is in its ability to transfer your ideas onto the canvas of your choice.
Are you thinking of an elaborate pattern on ceramics or a masterpiece on cloth? DTF printing provides a flexible and effective solution for that.
This printing method is an adaptable and effective method. It fosters creativity in pottery, textiles, and other mediums.
DTF Printing – Gear Up!
You start by utilizing a program like Adobe Photoshop to create a digital design. Then, you can print this pattern onto a unique translucent film using a DTF printer.
The film, which now has the design on it, goes through a crucial powder application process. This guarantees a successful transfer during the last phase of heat transfer. Using a heat press machine, You place the film on the intended surface. The ink and powder fuse with the material.
What’s the outcome? A robust and vibrant print that accurately captures the digital design. DTF printing has excellent color accuracy. It provides both beginners and experienced artists with many creative options.
What do You need to Get started?
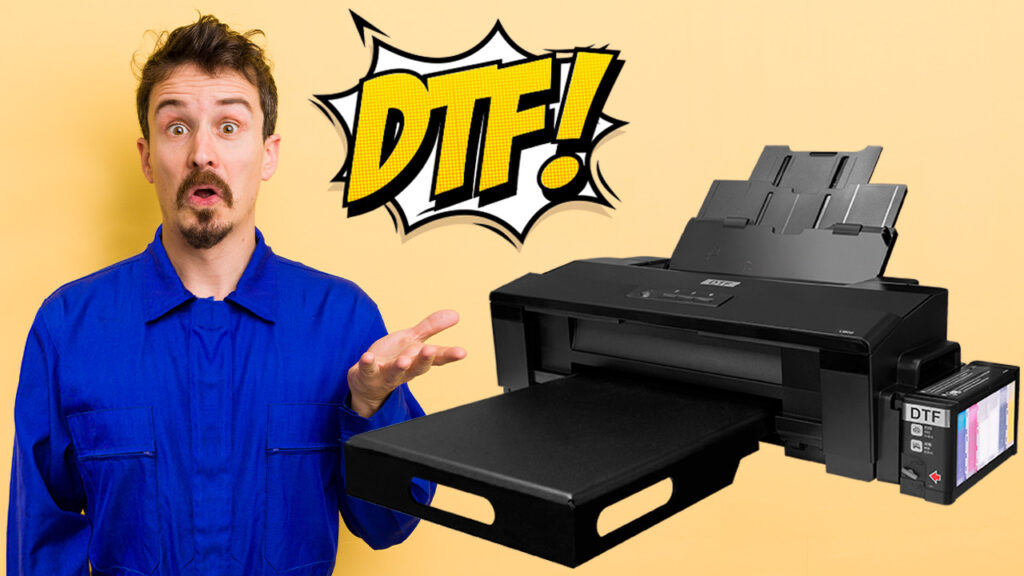
To begin DTF printing, you will need:
- DTF Printer:
Invest in a printer that can print DTF files. For beginners, brands like Epson or Ricoh are good choices.
- Graphic Design Software:
To produce your designs, use programs like Adobe Photoshop or CorelDRAW.
- Heat Press Machine:
Invest in a heat-transfer device. It guarantees the materials will embrace your ideas effectively.
- DTF Film:
This unique transparent film is what it is. It transfers your artwork from the printer onto the substrate.
- DTF Powder:
The transfer procedure requires powder. It aids in the ink’s adhesion to the surface. Select your preferred printing mediums, such as textiles, ceramics, or other materials.
DTF Printing: Understanding The Process
Now that you have the essentials, you can print your digital graphics. You can print your designs on a variety of surfaces! Thanks to the revolutionary DTF (direct-to-film) printing technique.
Using DTF Printing to its full potential requires an understanding of the process.
Let us walk you through it:
Digital Design Creation:
The initial stage of the DTF printing procedure is the production of digital designs. Graphic designing programs like Adobe Photoshop or CorelDRAW are used to create prints.
You can let your imagination run wild in this step. You can create complex patterns, vivid images, or logos with the help of these programs.
The digital design acts as your final print’s blueprint. It specifies the details and visual components that will be printed onto the surface. Here’s where you let your creativity run wild! You can now create the mood for the entire DTF printing procedure.
Film Printing:
Film printing uses a DTF printer to transfer a digital design to a transparent film. The film carries this design. It is crucial in the later phases of the DTF printing process.
Consider it as transferring your digital artwork onto a sheet of transparent material. The film helps to transfer the design onto the finished product. From printing on fabrics to ceramics, film printing is a crucial part.
The quality of the film printing plays a huge role in the accuracy of the transfer. With which fine details are transferred from the computer design to the surface.
Film Preparation:
The next step is to apply a coating of DTF powder after using a DTF printer to print your design on a specific film. To ensure adequate adhesion during heat transfer, this powder forms a bind with the ink. It improves the overall quality, producing printed material with rich colors and intricate details. For DTF printing to be successful, film preparation is essential.
Heat Transfer:
After printing on a film and adding DTF powder, the film goes on the material. A heat press machine is used. Heat and pressure make the ink and powder turn gaseous. This process sticks the design onto the fabric, creating a durable and colorful print. Heat transfer is crucial in making this happen.
The Outcome:
A bright, long-lasting print mirrors your original digital design.
DTF printing is renowned for its exceptional adaptability and color fidelity.
It turns your digital ideas into physical, colorful prints. This method is a favorite among artists and makers because it offers countless opportunities for expression across a range of mediums.
DTF Printing: What Materials Can You Print on?
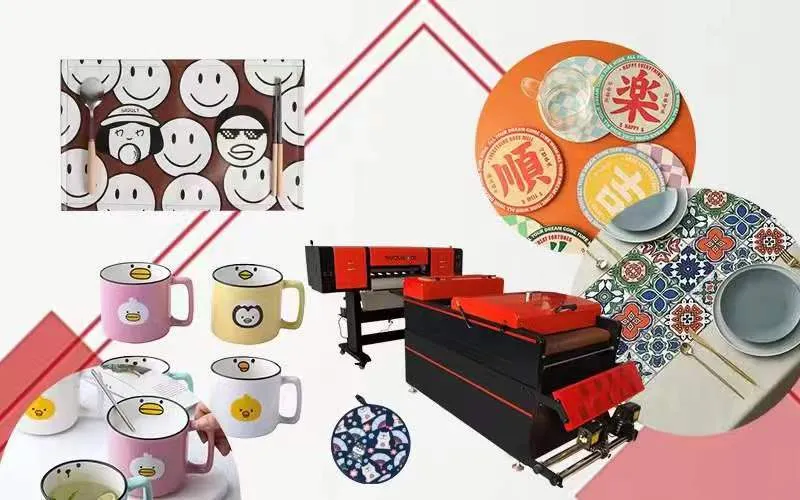
Material selection is a vital component of DTF (Direct to Film) printing. It affects both the versatility of this printing method and the quality of your prints.
Here’s a closer look at beginner-friendly material selection:
Fabrics:
Use fabrics as a canvas for colorful designs. Apparel, textiles, and accessories make a popular choice for DTF printing. When choosing printing materials, consider the fabric’s kind, weave, and color. Blends, polyester, and cotton are common choices.
Ceramics:
DTF printing is not limited to textiles. It can also be used to print elaborate designs on ceramic surfaces such as plates, mugs, and other items. Find out if your DTF printer can print on ceramic materials. You should also investigate the prerequisites for successful transfers.
Polyester:
Polyester textiles can successfully endure heat transfer and keep brilliant colors. This makes them a good choice for DTF printing. Polyester textiles are frequently utilized in clothing. Sportswear and a variety of promotional products are made with it!
Specialized Materials:
Traditional surfaces aren’t the only ones that are used for printing. You should examine specialty materials. Leather, wood, and some polymers that are made for particular uses can all be printed. Print success is ensured by being aware of these materials’ properties.
Material Pre-treatment:
Improve ink adherence and endurance by pre-treating certain materials before printing. Coatings or pre-treatment treatments aid in streamlining the printing process. If you’re printing on rough or difficult surfaces, pre-treating is the way to go!
Material Texture and Thickness:
Take into account the material’s texture and thickness. Textured surfaces can add dimension to your prints. Thicker materials need the heat press settings adjusted to achieve optimal ink penetration.
Durability and Washability:
Particularly for fabric applications, assess the material’s washability and durability. Designing long-lasting prints requires an understanding of how prints hold up to washing and regular use.
Post-Processing Requirements:
Post-processing requirements can vary depending on the type of material. For instance, fabric prints may need curing to set the ink and ensure colorfastness.
Post-Processing Requirements:
Consider how the materials you select will affect the environment. Sustainable and environmentally friendly choices are becoming more and more preferable in the printing sector. Examine resources that support your environmental beliefs.
Budgetary Considerations:
Pay close attention to your budget! Particularly while working on bigger projects or commercial ventures. Recognize the financial effects of various materials to learn the balance between price and quality.
DTF Printing Secrets: What Else You Should Know!
- Educate Yourself: To understand the dynamics of DTF printing, explore the subject! Study blogs, forums, and online courses. By understanding the procedure, you will become a proficient DTF printer. You’ll also be able to resolve typical problems.
- Select the Appropriate Printer: Select a DTF printer that fits your needs and price range. To make an informed choice, consider printing speed, resolution, and ease of maintenance.
- Try Different Designs: Begin with small designs and a variety of materials. This practical method steadily improves your skills. It will boost your confidence!
- Adjust Your Equipment: To produce great designs, learn how to adjust your machinery! Your printer and heat press machine should be adjusted according to your preferences. For best results, adhere to manufacturer instructions. Do routine maintenance. Join online forums and groups where DTF aficionados exchange ideas! Stay in touch with one another, and make new friends! You can learn so much from other people on your path.
Conclusion
Consider your journey as an artwork in the world of DTF printing. Start by reading internet tutorials. Pick a printer based on your requirements, and enjoy experimenting with various ideas.
Ensuring your music is in tune is similar to calibrating your equipment. Interacting with other members of the DTF community facilitates learning from one another. It’s about making something unique, not simply about printing.
You’re not simply joining the DTF printing world! You’re shaping it with confidence and friends at your side. There is so much more to explore and create in this vibrant realm of creativity.
Every print is like a piece of your tale!
This is about producing an engaging experience, not just printing. Thus, with measured confidence and a passionate network, you are not merely joining the DTF printing world; rather, you are influencing it.
Like what you read? Head on over to our blog and unlock a colorful world of knowledge about the creative universe of DTF Printing!