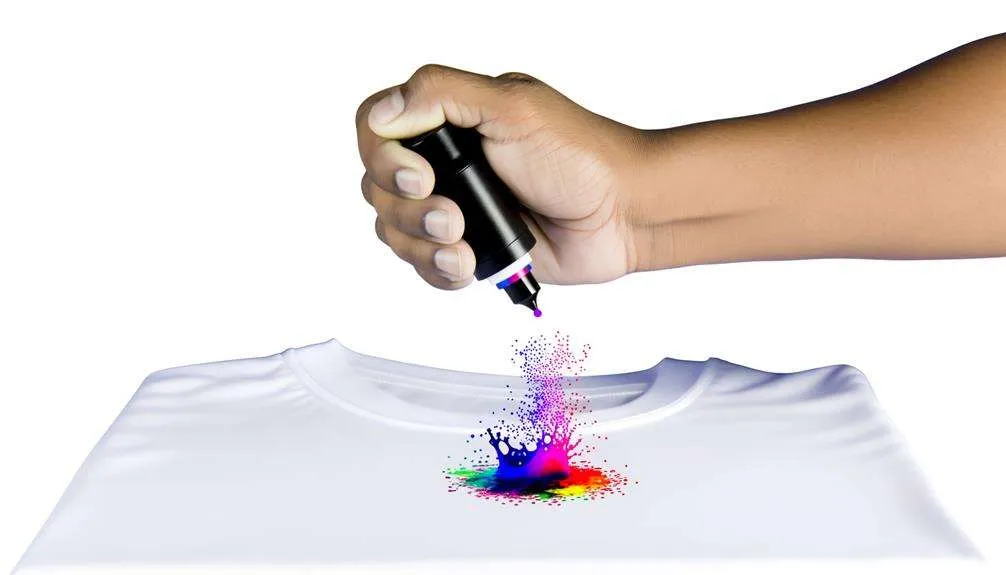
If you can’t wait to dive into the fascinating world of DTF printing, you’re in for a treat! Our step-by-step guide will prepare you to unleash your imagination onto textiles.
We’ll walk you through the process and get into the specifics. Including what you’ll need and essential factors to take into account.
And the subtleties that make DTF printing an exciting project.
Oh, and don’t forget to go through our Bonus Tips!
Ready? Let’s go!
Step 1 – Gather the Essentials for DTF Printing
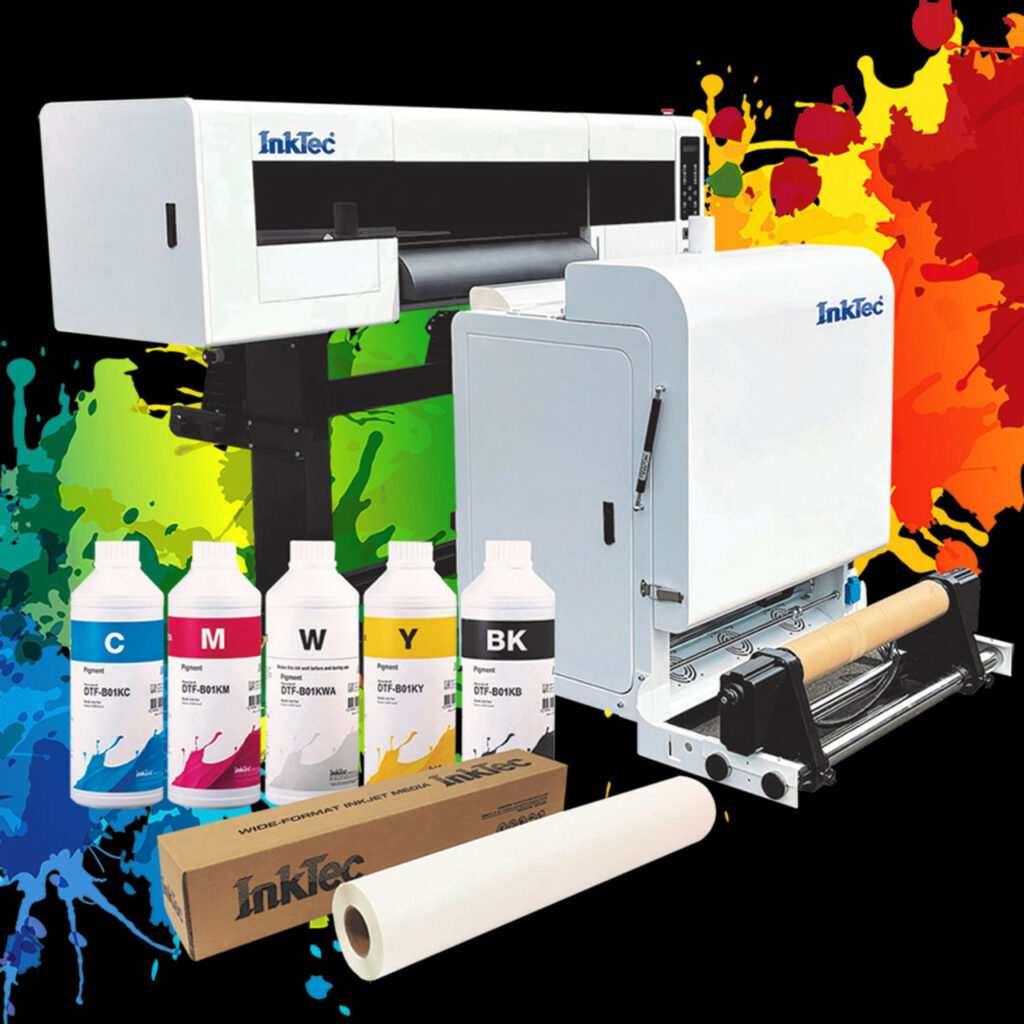
Begin by obtaining a set of necessary supplies and tools before getting started.
To guarantee a smooth and effective printing process, familiarize yourself with the essentials.
The following is a detailed list of everything you’ll need:
1- DTF Printer
Invest in a high-quality DTF printer. This step is crucial to achieve effective prints in the DTF printing process.
Here’s an elaborate breakdown of why the choice of a DTF printer matters:
- Efficient printing: DTF printers use sophisticated inkjet technologies that offer remarkable and accurate printing. These printers guarantee a superior finished product. DTF Replicating precise lines
- Color Precision: The cutting-edge technology of DTF printers makes precise color reproduction possible. This ensures meeting client and customer expectations through vibrant and lifelike prints.
- Flexibility: DTF printers are adaptable and suitable for various films and textiles. These printers offer endless creative options. These options range from experimenting with materials to crafting unique patterns.
- Consistency: When printing professionally, consistency is essential. A reliable DTF printer from reputable brands guarantees consistent performance over time. Maintaining the dependability and quality of your printing processes depends on this.
- Ease of Usage: Many DTF printers have intuitive user interfaces. These interfaces have simple settings and intuitive controls. These controls let beginners use them, making them understand the process easily.
2- DTF Ink:
Use specialized DTF inks that are compatible with your printer. These inks adhere to the film and transfer seamlessly to the fabric.
They adhere to DTF films, ensuring seamless transfers on different fabrics. These fabrics include cotton, polyester, and other blended fabrics.
Specialized DTF inks are essential in the Direct-to-Film (DTF) printing process. This is because they provide vital characteristics that improve print quality and longevity.
DTF ink strength endures numerous washing cycles, preserving the fabric’s quality.
DTF inks also offer quick drying times to facilitate productive production procedures. When choosing DTF inks, it’s critical to consider printer compatibility.
This ensures peak performance, ethical printing, color choice, ink efficiency, and brand integrity. It also ensures industry compliance. Selecting specialist DTF inks is essential to getting exceptional outcomes.
3- DTF Film:
These films are specifically made to work with DTF inks. Hence, guaranteeing maximum adherence and a seamless transfer onto fabric. DTF films come in rolls and different thicknesses to fit various printer sizes.
DTF films are also made to fit the design specifications. Their ability to hold little details helps produce crisp and clear prints precisely. The films are transparent, which helps with precise pattern placement. They load readily into printers.
4- Adhesive Powder:
An essential tool in DTF (Direct-to-Film) printing is adhesive powder. During the heat press process, heat activates this bonding agent.
It is then applied to the printed film. The adhesive powder helps to attach the design to the cloth.
For continuous adhesion, a uniform application is a must. You may print on various textiles thanks to its compatibility with many fabrics. Put your trust in adhesive powder to form a strong bond that will ensure the longevity of your prints. It’s essential to your success while printing DTF designs.
5- Heat Press Machine:
A heat press machine is your powerhouse in DTF (Direct-to-Film) printing. This machine is pivotal in transferring your designs from film to fabric.
This essential equipment applies heat and pressure to your fabric. The pressure then activates the adhesive. This ensures a seamless bond between the ink and the material.
Invest in a reliable heat press with precise temperature and pressure controls. By doing this, you’ll ensure consistent and professional results.
It doesn’t matter if you’re working on apparel, accessories, or promotional items. This heat press machine is your go-to for bringing your designs to life.
6- Graphic Design Software:
Your creative journey in DTF printing begins with graphic design software. This software empowers you to craft high-resolution digital designs. Complete with intricate details and vibrant colors. Platforms like Adobe Photoshop or CorelDRAW are great to use if you want to create designs. These software tools are your canvas. They allow you to bring imagination to reality and set the stage for stunning prints in the DTF process.
Aim for a resolution of 300 dpi to ensure sharpness and clarity in your prints. Adjust colors in a precise manner and determine size and placement. Let your creativity flow!
7- Work Area and Airflow:
Establish a special work area with enough ventilation. A well-ventilated space is essential to a secure work environment. Since DTF printing calls for the use of sticky powders and inks.
8- Gloves and Safety Equipment:
When handling inks and adhesives during printing, take extra precautions. Keep yourself safe. wear gloves and other protective clothing like goggles and masks.
9- Curing Tools:
Depending on how you set things up, you could need curing tools like a heat press or a conveyor drier. Curing is necessary to guarantee a long-lasting print and improve color permanence.
10- Downloadable Software:
RIP (Raster Image Processor) is a well-liked software that is downloadable. It can help you get the best possible color management and print quality. RIP software ensures accurate color reproduction and printing process control.
11- Manufacturer Recommendations:
See and abide by the instructions supplied by the manufacturers. Pay close attention to the manuals! By doing this, you’ll ensure the best results and equipment longevity.
Ensure you have these necessary supplies and tools! You’ll be ready to explore the fascinating field of DTF printing. And let your imagination run wild with fabrics.
Step 2 – Design Your Digital Print
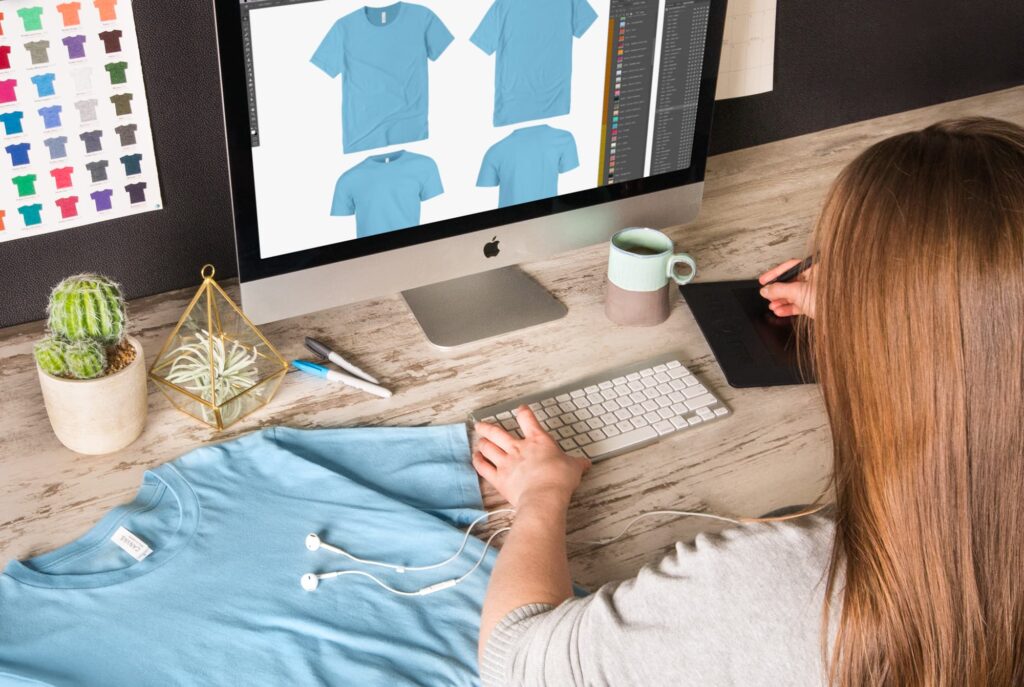
Kickstart the creative process by crafting a digital design. This is the second step of your DTF printing journey!
To achieve optimal results, adhere to these key considerations:
- Resolution: Set a high-resolution standard for your graphics, targeting 300 dpi (dots per inch). Setting this standard ensures that your prints exhibit sharpness and clarity. At the same time, it also precisely captures intricate details.
- Color Calibration: Fine-tune your color palette with precision in your design software. Accurate color calibration is paramount to achieving the desired vibrancy. Right when the design is transferred onto the fabric, ensure your prints pop with life.
- Size and Placement: Deliberate on the size and placement of your design on the fabric. Consider the dimensions of your DTF printer. You must also consider the dimensions of the specific textile you are working with. Thoughtful consideration of these factors ensures a seamless and visually appealing transfer of your digital creation onto the chosen canvas. Let your design shine with clarity, vivid colors, and strategic positioning.
Step 3 – Film Printing
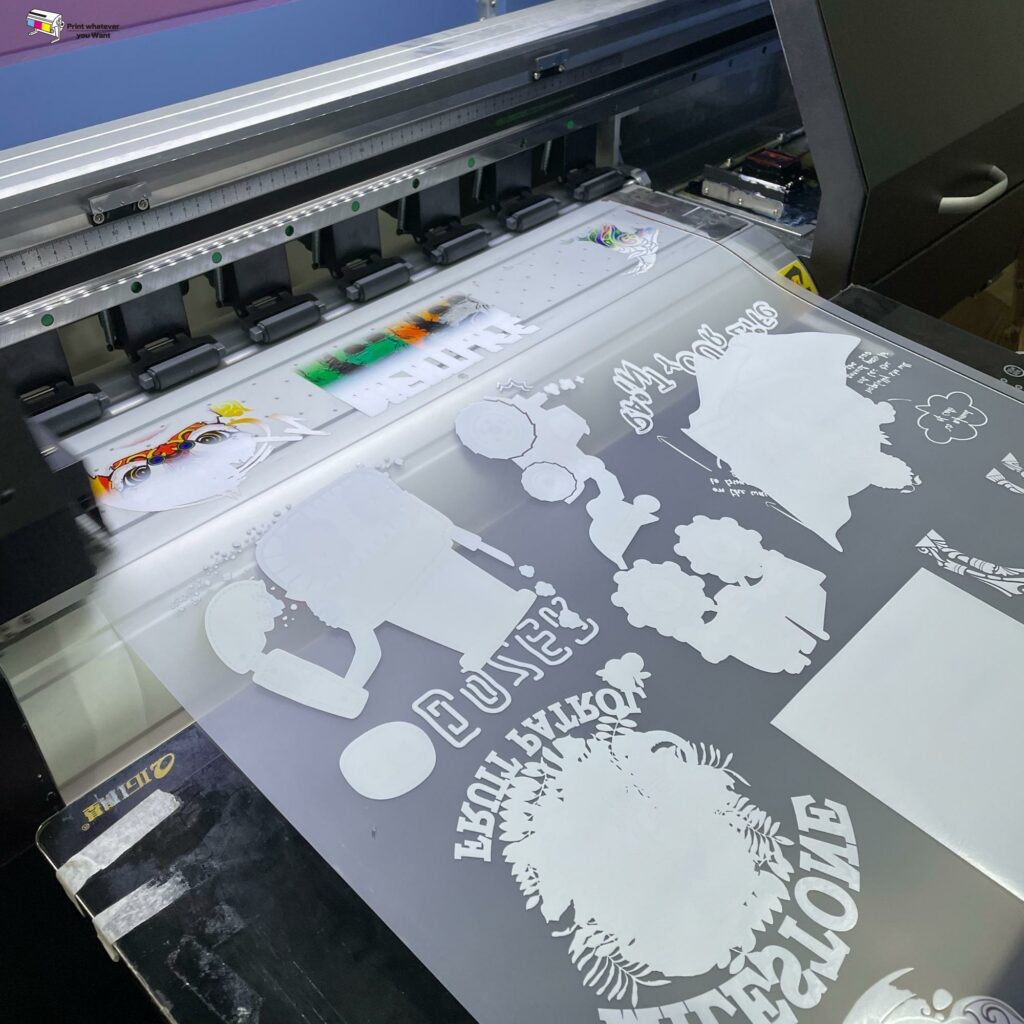
Moving from design creation to film printing is vital.
Now, let’s proceed to the third stage of your DTF printing process.
For a smooth procedure, adhere to these reduced steps:
- Load DTF Film: Insert the DTF film into your printer. Ensure it complies with your particular printer’s specifications.
- Print Settings: Adjust the following best to fit the requirements of your design and the cloth:
- Resolution
- Color profile
- Printing Process: Begin the printing process by supervising the film. Ensure that it catches all the minute details of your design. This stage establishes the basis for the later phases of the DTF printing process. It turns your digital creation into a physical form.
Step 4 – Apply Adhesive
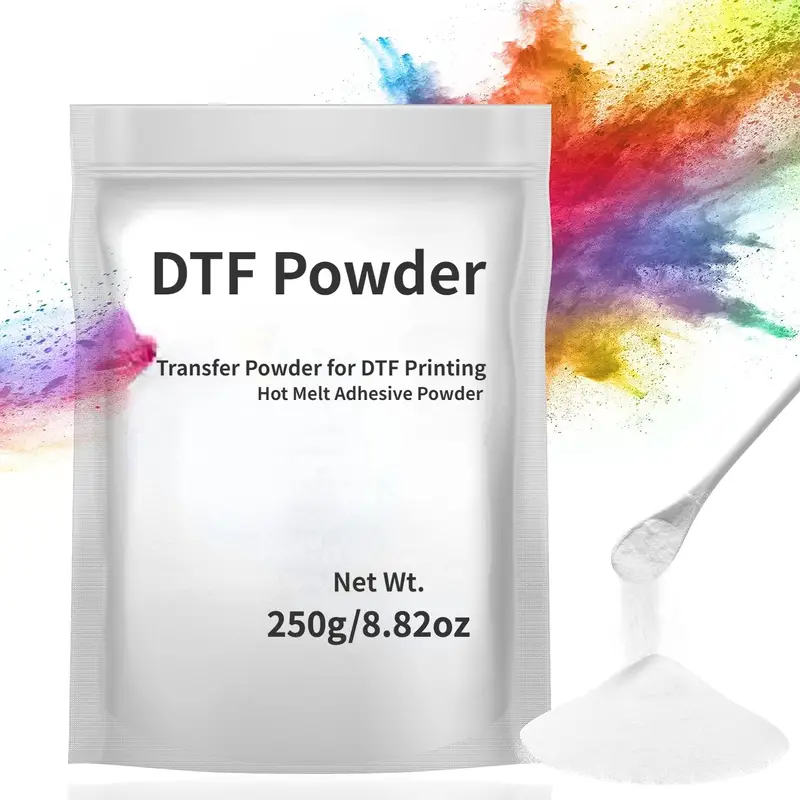
When you reach the fourth stage of your DTF printing process, apply the adhesive to the printed film.
Here are some critical steps to remember:
- Even Application: Ensure that you apply the adhesive over the entire printed surface. The application should be thin and even. Doing this will guarantee a smooth transfer. It will also improve the overall quality of your prints.
- Drying Time: Give the adhesive enough time to completely dry before moving on to the next step. This is an essential step! Because it guarantees that the adhesive is prepared for the heat press process. This process lays the groundwork for a successful design transfer onto the fabric.
Step 5 – Transfer to Fabric

Start the exciting fifth part of your DTF printing adventure! By carefully and precisely transferring your design to the cloth.
To ensure a successful transfer, adhere to these crucial steps:
- Cloth Preparation: Make sure the fabric is spotless and ready to accept your pattern before transferring it. Remove all lint and wrinkles to prepare the surface for the next transfer.
- Positioning: Carefully apply the adhesive-coated film to the cloth, making sure it is just where you want it to be in the pattern.
- Heat and Pressure: To apply the ideal amount of heat and pressure, turn on the heat press machine. Together, they activate the adhesive. Heat and pressure ensure the smooth transition of your design from the film to the fabric. This transformative step brings your digital creation to life on your chosen textile. It marks the culmination of your DTF printing process.
Step 6 – Peeling and Curing
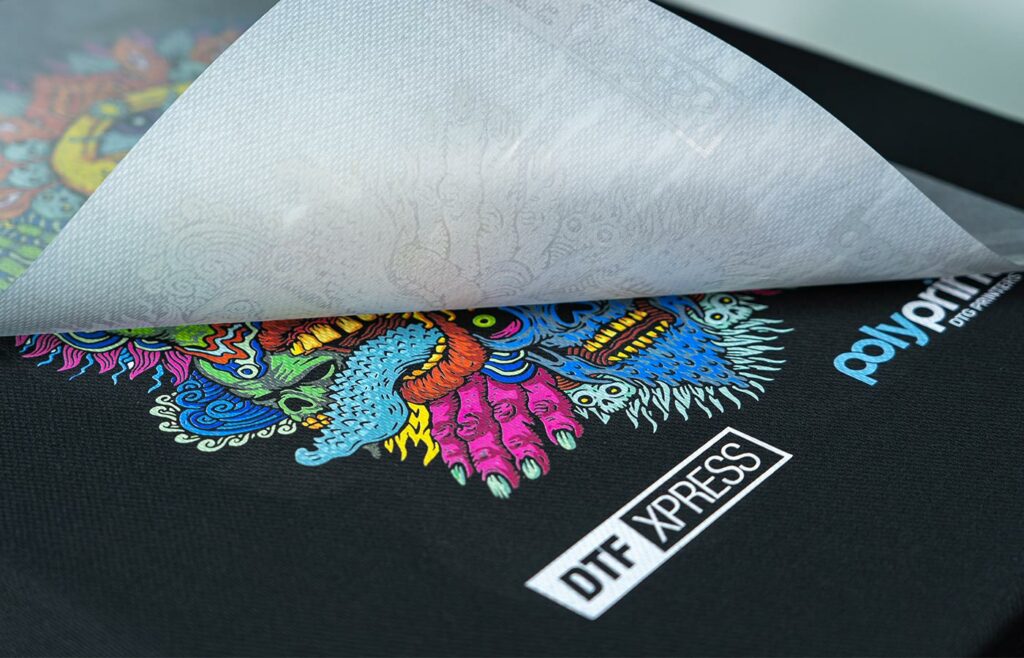
Welcome to the final stages of your DTF printing process! Carefully remove the film and enhance the durability of your print’s precision:
- Peeling Process: Gently remove the film to reveal the beautiful design seeped deep into the cloth. This phase is the last in your complex printing procedure! this is where you can see the finished product of your digital design.
- Curing: Apply a curing technique to the printed fabric to increase its durability.
Adhesives adhere to the suggested temperature and duration limits. These limits improve color robustness and guarantee a print that lasts.
These finishing touches ensure that your DTF print is ready.
Step 7 – Last-Minute Inspections and Quality Control
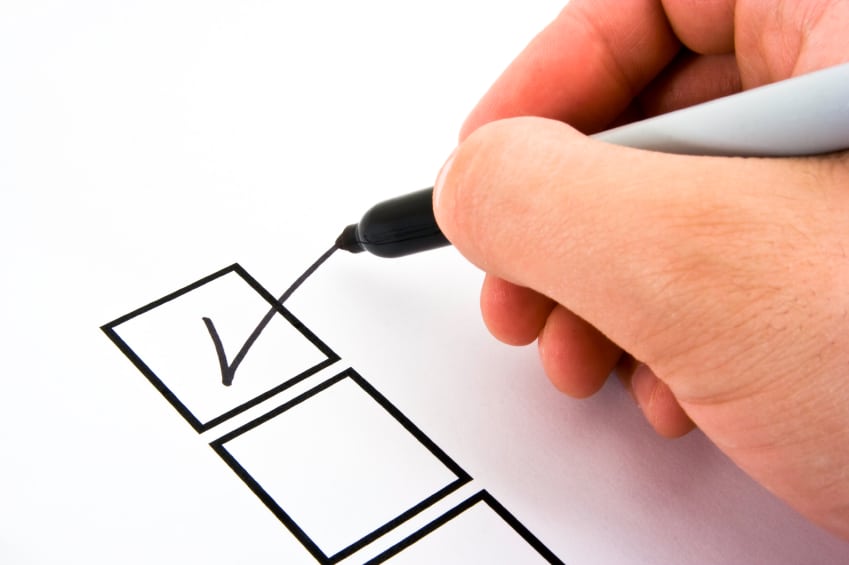
- Examine the Print: Examine the printed cloth for overall quality, color vibrancy, and detail preservation. Verify that the design has been successfully transferred.
- Cut and Coat:
Trim any extra film or threads from the printed fabric to give your DTF print a polished appearance.
Things to Consider When Selecting a DTF Printer
Dimensions and Resolution of the Print:
Think about the largest print size and resolution a DTF printer can produce. Ensure it fits your unique printing requirements.
This is especially important if you’re working on larger or more intricate designs.
Compatibility of Ink:
Make sure that you verify whether the DTF printer is compatible with the specific DTF inks. You can use the recommended inks below to guarantee best results and longevity:
- NeoFlex DTF Inks:
- NeoFlex DTF inks are favored by many in the industry. They are known for their vibrant colors and compatibility with various DTF printers.
- NeoFlex DTF inks are favored by many in the industry. They are known for their vibrant colors and compatibility with various DTF printers.
- Dupont DTF Ink:
- Dupont is a trusted name in the printing industry. Their DTF inks are recognized for their color accuracy and durability.
- Dupont is a trusted name in the printing industry. Their DTF inks are recognized for their color accuracy and durability.
- UV DTF Inks:
- Some DTF printers are designed to work with UV ink. This provides additional options for those seeking specific characteristics. Options include quick curing and high resistance.
Easy Maintenance:
Select a DTF printer that requires less upkeep. Regular maintenance is essential for your equipment to last a long time.
Regular maintenance also ensures your machines work and operate consistently.
Adaptability to change:
Think about the possibilities for upcoming improvements and technological breakthroughs.
Use a DTF printer that supports firmware updates and hardware upgrades. This will help to keep your equipment up to date.
User Evaluations and Suggestions:
First, research user reviews and seek advice from colleagues in the field. Second, real-world experiences can provide valuable insights.
Lastly, focus on assessing the functionality, dependability, and usability of specific DTF printer models.
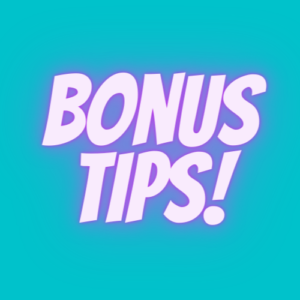
Here are some bonus tips to enhance your DTF printing experience and ensure optimal results:
Bonus Tip 1: Experiment with Different Fabrics
Don’t limit yourself to a single type of fabric. DTF printing is versatile. It works well on various materials, including cotton, polyester, and blends. Experiment with different fabric types. This way, you’ll be able to discover the unique qualities of each. You can then fine-tune your printing settings accordingly.
Bonus Tip 2: Conduct Test Prints
Before committing to a large print run, always conduct test prints on scraps of your chosen fabric. This allows you to:
- Adjust setting
- Test color accuracy
- Ensure the final print meets your expectations. It’s a crucial step in avoiding potential issues during a full production run.
Bonus Tip 3: Use RIP Software for Color Management
Consider investing in RIP (Raster Image Processor) software. Softwares like this enable you to enhance color management.
You’ll be able to control the printing process. RIP software can optimize color accuracy, increase sharpness, and improve overall print quality.
Bonus Tip 4: Optimize Ink Density
Experiment with ink density settings. Doing this will help you to find the right balance for your specific design and fabric.
Adjusting ink density can:
- Influence color vibrancy
- Saturation
Bonus Tip 5: Maintain a Clean Workspace
Regularly clean your DTF printer, heat press machine, and surrounding workspace.
Dust and debris can negatively impact print quality. Therefore, maintaining a clean environment is essential for consistent and high-quality results.
Bonus Tip 6: Explore Specialty Inks
Consider using specialty DTF inks. Fluorescent or metallic inks to add unique effects to your designs.
These specialty inks can make your prints stand out. They can also provide additional creative possibilities.
Bonus Tip 7: Stay Updated on Technology
Keep abreast of advancements in DTF printing technology. Manufacturers often release updates or new equipment.
Newly released equipment is upgraded each time. These updates can enhance efficiency, speed, and print quality.
Staying informed ensures you’re utilizing the latest tools available in the industry.
Bonus Tip 8: Network with Other DTF Enthusiasts
Connect with other DTF printing enthusiasts.
You can do this either through online forums, social media groups, or local industry events.
Sharing experiences, tips, and troubleshooting advice with a community can provide valuable insights.
This will also help you overcome challenges.
Bonus Tip 9: Invest in a Quality Heat Press
Your heat press machine is a crucial component of the DTF printing process.
Invest in a quality heat press with accurate temperature and pressure controls.
A reliable heat press ensures consistent and even heat distribution. Hence, contributing to successful transfers.
Bonus Tip 10: Document Your Settings and Experiments
Keep a detailed record of your printing settings, experiments, and successful outcomes.
This documentation becomes a valuable reference for future projects and troubleshooting. It helps you replicate successful prints and avoid pitfalls.
Incorporate these bonus tips into your DTF printing journey. You’ll not only improve your skills but also open up new creative avenues.
Remember that experimentation is key! And each print provides an opportunity to refine and perfect your craft.
The Finale
To sum up, DTF printing success hinges on precise equipment selection. Quality films and inks amplify your final prints.
Calibrate settings meticulously for optimal outcomes. Prioritize effective pre-treatment to enhance substrate adherence.
Follow a systematic workflow, from design to finishing touches. Regular maintenance ensures smooth printing operations.
Stay updated on industry advancements for continuous improvement. Network with peers for valuable insights and troubleshooting.
Embrace experimentation to unleash the full creative potential of DTF printing.
Master the process, stay adaptable, and enjoy the vibrant, customized results.
Happy printing!